A simple and inexpensive tool to cut large graphite rocket nozzles. If you find yourself without or unable to use a large lathe or mill to cut graphite, this tool brings the rigidity needed to cut accurate nozzles using a drill press for power.
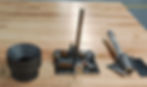
Disassembled cutter with nozzle: The base aluminum plate holds a hardened steel shaft with four screws for locking the graphite into place. The blade holder spins on the shaft cutting with interchangeable tool steel blades customized for each cut. There is also an un-pictured blade for the throat cutting.

Assembled cutter with both angle blades mounted.
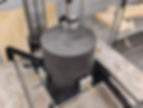
With the center shaft removed, the graphite round is locked into place and the base clamped to the drill press. A large woodworking bit is used to hollow out the center of the round, the hole must be smaller than the desired throat diameter, exact centering is not critical.

After the center hole is cut, the central shaft and cutter holder are reinstalled. A magnetic dial indicator and shims are used to center the round. The four radial screws are used like a four jaw chuck. Large bottom shims are recommended to give the graphite dust a gap to be vacuumed out from. Note the cutter is installed upside down to not cut during centering.

With the round centered the cutting can begin, starting with the throat and followed up by the angled sections.
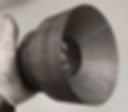
Freshly cut nozzle, the sharp inner transitions can be hand smoothed as needed.

Gentile and repeated cuts on a bandsaw with a backstop can be used to add an external step to the nozzle. Yes, this was mid processing and the rough ends were cut off for the final product.
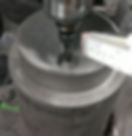
We have used a CNC mill for large nozzle cutting in the past but much to our and the owner's chagrin, we turned his shop and our noses into a coal mine despite two shop vacs.

This tool certainly has room for improvement, as it was made on short notice with no budget and only scraps we had laying around. A few notes on the design:
The tool holder was made two faced and of Chromoly which is overkill.
The bushings were made of 360 Brass, bronze bushings might be better.
Tool steel blades are great but also not necessary.
Cylinders can be fit to the shaft as end stops to prevent cutting too deep.