Supersonic rocket flight demands a durable nose cone tip, we went for overkill and opted for Inconel. Straight angled cones are simple enough to make on a manual lathe, but a Von Karman profile is a tad harder. Those with CNCs would have to eat the cost of Inconel round stock, but we were lucky enough to have access to a Markforged Metal X printer with Inconel 625.

3D printing allows us to make a hollow cone, minimizing the use of expensive material and allowing us to easily fill with ballast lead as needed.

The layer lines are easily ground away with a belt grinder.
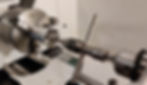
The base is threaded with aggressive cuts and a fresh tap as the Inconel likes to work harden.
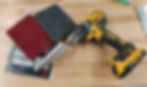
With a bolt in the threaded base the tip can be spun in a drill for wet sanding and polishing with a scotchbrite pad.

Cross section of the CAD.
Design and printing notes:
The internal cone under the top dome has its angle set to prevent the generation of supports while still minimizing material.
The cone base is thickened to counteract shrinkage and warping
The cone's thickness is set to prevent infill and only use wall lines with no gaps
Print on a raft because the Metal X printer has terrible elephants foot

These tips are astonishingly durable, this cone's rocket failed to deploy its parachutes and slammed into the hard packed desert floor from over a mile up. The only damage to the tip is from the threaded rod in the rear bowing in the base spokes.