
With some relatively simple supplies you can make your own beautiful engagement ring at home. The above is a version made with moissanites and needle tumbled which brings out a copper tone to the silver.

This one ended up with an extra touch of handmade feel to it with some tool-marks around the larger flush set emeralds.
My now wife wanted a custom engagement ring and I was up for the challenge. I've always enjoyed pushing my comfort zone and acquiring the needed skills to complete a time sensitive project. I was issued a handful of Pinterest pictures for inspiration, a family diamond for main stone, and set off to designing.

Six thick prongs secure the center diamond for high durability. She wanted leaves up the sides with green stones set between them. This CAD model was designed without the stones for simplicity, but with some features to make the final processing easier. The side gem slots had starter holes for easy centering, and the prongs were pre-notched as markers for a level diamond setting.
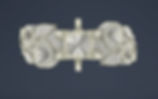
Top view shows non-mirror symmetry of the leaves. This makes the ring look exactly the same no matter how you put it on.
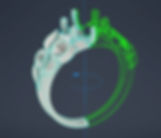
CAD tip: Using a circular pattern turned out to be the best way to make symmetrical but non mirrored design.

From test piece to metal: I used my resin printer to make test rings, along with the purple wax rings for the actual casting process.
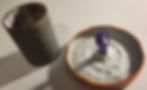
Casting can be done quite cheap with a section of steel pipe, and some modeling clay to hold the wax in place. I used proper investment, however improvised the burn out in a propane grill for an hour. It worked fine...

Simple casting setup. The vacuum pump "sucks" the molten metal into all the details of the mold.

I designed and 3D printed an expanding ring vice to hold the ring as I drilled holes and set stones. Tightening the wing nut pulls the screw into the ribbed section, expanding it to hold the ring in place.