These are a few old designs for small high power APCP rocket motors with a variety of thermal liner/grain casing materials. This post will focus on the liners/castings used. The following materials and techniques have worked well with 1-3.5" ID motors. We have even flown a 4.5" motor which managed Mach 3, but that design was pushing the limits. I have new designs for even better motors but wanted to share some things that worked so far.
This is not a comprehensive guide on high power solid rocket motor design or construction, just sharing some of my experience with certain construction techniques.
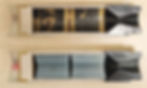
First we'll note the motor commonalities and then show the different liner solutions. The above cross sections came from successfully fired motors, the bottom one is refilled with inert propellant.
These motors all use APCP with BATES style grains.
The propellant casing also serves as the ablative thermal liner.
Tubes are roll wrapped on PVC pipe and generally made of E or S fiberglass.
The motors are generally referred to by their matching nominal PVC diameter. Ex: A "3 inch motor" is actually a 3.5" ID motor made on 3" PVC
Epoxy is used for sealing and holding everything in place.
Nozzles are made from fine or medium grain graphite.
Forward closures, from hereon out "bulkheads" are made from machined XX Phenolic or cast MSC
"MSC" is short for MicroSphere Composite, a mixture of glass micro balloons bound into epoxy, polyester, or polyurethane.
PVC Lined Motors:

With the thrust chamber roll wrapped around PVC pipe, sections of PVC are a perfect fit for propellant castings. The ID can be bored out to make room for more propellant. The bulkhead and spacing ring are turned from phenolic.

This cross section shows a 3.5" ID motor after firing, notice that the PVC has warped and separated from the walls. The warping only occurred after the motor extinguished when there was no more internal pressure holding it to the walls. The nozzle is potted in MSC, motors beyond 2" diameter often burn long enough to require nozzle insulation.
MSC Machined Liners:
MSC is significantly less dense than PVC and can have its properties fine-tuned with different quantities of microspheres and different resins.

This is an SEM image of an MSC shard. The hollow spheres reduce the density of the composite and provide insulation during the burns. Sometimes the micro balloons pop under the SEM's high vacuum.

To make the liner, polyester MSC is poured into an oversized 3D printed mold, once cured, the OD and chamfers are machined to spec.
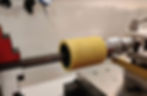
The 3D printed mold has its insides designed to accept a hexagonal shaft and live center for mounting on the lathe.

Once machined, the print is softened with a blowtorch or heat gun and worked out of the liner.
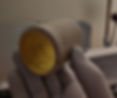
The final liner can be inspected for bubbles and defects with a flashlight in a dark room. This liner was designed with a large margin of error so the small surface bubbles are acceptable.

Four inch MSC machined liners filled with propellant prior to motor assembly.
MSC Rolled Liners:
Instead of wasteful machining and printing of molds, we can use a fiberglass tube identical to the motor ID for spin casting, aka "rolling" liners.
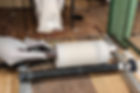
The fiberglass tube is filled with MSC and rolled to spread it evenly until cured. The MSC is poured from its mixing cup into a newspaper guide which dispenses into the spinning tube. The fiberglass is waxed to prevent sticking of the MSC and to fill in small tube defects.

This is a finished spin cast liner with its chamfered PVC end rings. The rings set the length and cast the needed chamfers. The final liner just needs bubble inspection and to have its chamfers cleaned of any release agent.
Note: For larger liners, MSC binders with high shrinkage are not advisable. One may be able to overcome this by characterizing the shrinkage and designing and oversize casting tube.
Grain Preparation:

Small diameter PVC grains are cast and then have their cores drilled out. A 3D printed jig is helpful to ensure concentricity when drilling.

Larger diameter grains are cast with a removable rod in the center which is held in place by a printed base. A sharpened putty knife makes for easy trimming of the propellant ends. We write the tare weight of liners before filling and the total mass once filled and trimmed.
Design and Assembly Notes:

The use of chamfers on internal components makes for easy assembly:
Pot the bulkhead into place with epoxy.
Once cured, stand the motor on the bulkhead end. Fill the male chamfer with epoxy. We call this "filling the moat."
The female chamfer of the next component is slid into the moat.
Rinse and repeat as needed for the next liners and nozzle
Finally pot the nozzle into place by filling it's external "moat."
Notes:
Ideally the female chamfer is cut to a sharper angle than the male, this helps push any bubbles out of the epoxy and prevents a glue starved joint.
The moats don't need to be filled completely with epoxy as the chamfer will take up most of the space once pressed in.
Older motors used spacers, but chamfered propellant grains remove these components.

X-ray of a spent motor's bulkhead and PVC liner interface. The PVC liners were used before the development of MSC liners and chamfers. To get a good seal between the PVC's flat face and its neighboring components, epoxy is applied around the wall of the motor such that the PVC will scrape the epoxy off when pressed into final position. This scraping prevents the entrapment of bubbles in the seal.
A variety of improvements can be made, especially for use in larger motors. One might consider the following:
A full length spin cast flexible liner
Fasteners
Flexible seals
More rigid tubes: Ex, carbon fiber, unidirectional reinforcement, filament winding, thicker tubes.
Bulkheads cast as part of the liner